NEWS | SOFTWARE | SHEET
Alternatives of Sand in Concrete Mixture
Unquestionably, one of the most crucial materials in the building industry is concrete. It is made of cement and both coarse and fine particles. One of the main components needed to make concrete is river sand. It is essential to the Mix's design as well. River sand is naturally occurring and is frequently extracted from the river banks or river beds.
Due to erosion, forest loss, and other environmental problems, sand supply has recently become extremely scarce. River sand is in short supply in the majority of the world due to the tremendous rise in sand demand brought on by the construction industry's explosive expansion.
Currently, the inaccessibility of river sand and the requirement for concrete to be manufactured at a lower cost have resulted in the development of a new substitute for river sand in concrete. This is why searching for alternatives to sand have become a very important part of the construction industry over the past few decades.
Lists of Substances to act as a Replacement for Sand
Artificial or M-sand: M-Sand is recognized as a substitute for river sand due to the decrease in high-quality river sand. Manufactured sand is referred to as M-sand. It is produced in factories or quarries by reducing bigger aggregate components like rocks or quarry stones to sand-sized fragments. There are many acceptable grades of M-sand utilized for various building projects.
M-sand is regarded as the greatest construction material recently found because of its many benefits. As a result, it has greatly helped the building sector find a long-term solution to the river sand problem. But the most important thing is to make sure that the M-sand is obtained from a trustworthy source and should be properly processed.
Benefits of Artificial or M-sand
- High flexural and compressive strength.
- Does not include marine items, oversized materials, or silt.
- Because the sand contains little or no moisture, there is no concern about its bulking up.
GGBS Materials: Iron and steel manufacturing leaves behind ground-granulated blast furnace slag. It is produced by putting the molten iron slag from the blast furnace into a stream or body of water to cool it.
These crystalline and glassy materials are then dried and processed into a fine powder that may be used in place of sand. Granulated blast furnace slag has a comparable particle size to sand.
So, GGBS may be used in concrete as a partial replacement for sand. However, the workability of all replacement levels has also decreased. A reasonable amount of chemical admixtures, such as superplasticizers, can be added to the mixture to boost its workability.
Benefits of GGBS Materials
- Concrete is given stronger compression strength by this additive.
- Exceptionally durability.
Bottom Ash Materials: In pulverized coal furnaces, the bottom ash is an agglomerated ash particle, and it may be found at the thermal power plant. It usually has an angular form and is grey to black in color. On the surface, it has a porous structure. Concrete is washed with bottom ash to remove the carbon and undesirable materials.
In this case, the replacement of the river sand in the concrete mix with washed bottom ash only resulted in an improvement in the concrete's qualities, but not its durability. A concrete compound made from washed bottom ash is less expensive than conventional concrete since river sand is replaced with washed bottom ash.
Benefits of Bottom Ash Materials
- The strength of concrete is increased when split tensile is added.
- As concrete density increases, it becomes more durable.
Powder of Sheet Glass as an Alternative: Considering that glass has a high silica content, it is an amorphous material that is partially pozzolanic under certain conditions due to its high silica content. In windows and doors, sheets of glass are used for the display of objects, and once they are broken, they are not able to be repaired.
It is therefore advisable to powder this material and use it as a substitute for sand in any concrete mixture instead of sand. There is an aesthetic appeal to the concrete that is enhanced by the use of recycled glass powder.
Benefits of Powder of Sheet Glass
- Strengthens concrete by increasing compressive strength.
- An increase in tensile strength is observed.
Quarry Dust Materials: Quarry dust has some potential as a fine aggregate substitute for river sand in the construction of concrete. It is essentially a by-product of stone crushers created during the coarse aggregate crushing and screening process.
The compressive strength of the concrete is somewhat improved when quarry dust is used in place of river sand. This, when combined with elements like fly ash, results in even superior workability and strength.
To get more clear ideas, go through the following exclusive construction video tutorial.
Lecturer: Engineering Motive
To give the concrete additional strength, it needs to be carefully screened and treated. Quarry dust is widely accessible and practical to utilize.
Benefits of Quarry Dust Materials
- A high degree of permeability.
- Strengthened by high compression.
- Enhances the efficiency of work.
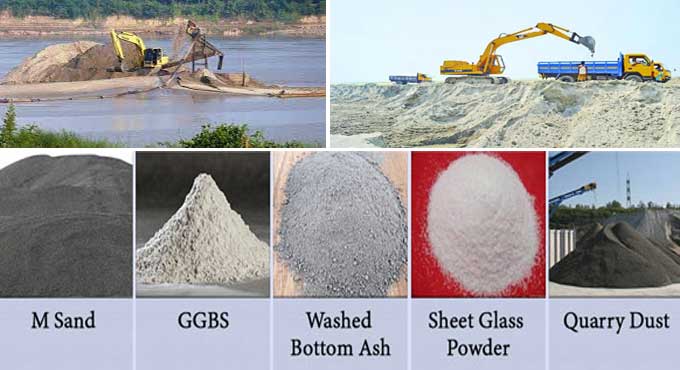