NEWS | SOFTWARE | SHEET
The 10 Types of Concrete you should consider in 2023
A concrete mixture consists of cement, fine aggregates, and coarse aggregates, mixed with water. When cement and water are mixed properly, they start a reaction that bonds together and produces a plastic mass, which hardens over time as concrete.
It depends on the quantity and proportions of the ingredients in concrete to obtain its properties. Cement types can also have a significant impact on the properties of the mix.
The strength of concrete in compression is very high, but it is very weak in tension. Depending on shape and size, fresh concrete can be poured into any appropriate form or mold. In construction work such as buildings, bridges, dams, roads, and flyovers, concrete is widely used.
Concrete Types
Plain Cement Concrete (PCC)
Cement, fine aggregates, coarse aggregates, admixtures and water are the basic ingredients of plain cement concrete. The strength of PCC in compression is very high. It is very weak in tension since it lacks reinforcements like steel.
According to the mix design ratio of PCC used in foundations for buildings, it is 1:2:4 and 1:3:6. As soon as the hard strata have been reached, sand is laid followed by Plain Cement Concrete. The footing reinforcement cage is then placed above the Plain Cement Concrete.
Reinforced Cement Concrete (RCC)
Cement, aggregates, additives and steel reinforcements are the main materials of reinforcement cement concrete. Reinforcing plain cement concrete with steel is a simple process.
Reinforced cement concrete overcomes all the limitations of plain cement concrete. Because steel has a nearly identical thermal coefficient of expansion as all other metals, it makes the best reinforcement material.
Steel has a thermal coefficient of 12 per centigrade, whereas concrete has a thermal coefficient of 14.5 per centigrade. Steel has this property, which makes it more compatible with concrete than other metals.
Fiber Reinforcement Concrete
An example of fiber reinforced concrete is made using cement, water, aggregates, and flat or rounded fibers. A variety of fibers can be used to reduce permeability, bleeding, and cracking, including steel, polypropylene, glass, asbestos, carbon, and organic fibers.
A ratio of .1% to 3% of the total volume of the concrete is added with fibers. Fiber dimensions are represented using the term aspect ratio, which is defined as the ratio between their length and diameter.
Since the orientation of the fibres is mostly random, the aspect ratio ranges 30 to 150. Depending on the design criteria, they can be oriented parallel or perpendicular to each other.
Glass Fiber Reinforcement Concrete
Cement, water, aggregates, and glass fibers are the main components of glass fiber reinforced concrete. In terms of tensile strength, glass fibers have an approximate value of 4080 N/mm2.
Additionally, the alkaline nature of the glass fibers makes the structure more durable. Glass fibers are one of the most affordable reinforcements, making the structure more cost effective.
As with fiber reinforced concrete, glass fiber reinforced concrete has similar properties, applications, advantages, and disadvantages.
Ferro Concrete
It consists of cement, fine aggregates, chicken wire mesh, and water, and is also known as Ferro concrete.
Firstly, tight packed wire mesh is installed over which a mix of rich cement mortar is applied in a ratio of 1:2 or 1:3. In the wire mesh, holes should not be larger than 1 mm in diameter. Plastering, centrifuging, mechanically forming, or guniting can be used to apply mortar to wire mesh.
Ready Mix Concrete
A ready mix concrete is a concrete made from cement, aggregates, water, and admixtures in a factory and delivered to the job site. Concrete that is ready mixed is preferred when storage and mixing space are limited.
Transit mixers, which rotate continuously and prevent setting, take plant made concrete and load it into special delivery trucks called transit mixers.
To give allowance for transportation and placement of the concrete, retarders are usually added to the concrete mix to slow down the setting process. Both factory and site quality checks are carried out.
Precast Concrete
Cranes are used for erection of precast concrete structures after they have been cast, cured, transported to the site, and assembled. A reinforced cage is inserted inside each mould as reinforcement for the precast structures.
Depending on the requirements, they may or may not be pre-stressed as the dried concrete members are cured under controlled conditions. Members are provided with hooks that permit them to lift each other. During erection and handling, precast members are designed to take into account potential stresses.
High Density Concrete
A high density concrete consists of cement, water, fine aggregates, coarse aggregates, and high density aggregates. Concrete with a normal density of 2400 kg/m3 is called Plain cement concrete. Depending on the density, high density concrete can weigh between 3360 and 3840 kilograms per cubic meter.
Densifying concrete involves increasing cement content, reducing voids, and adding aggregates of high density like barite, magnetite, serpentine, limonite, and goethite.
High Performance Concrete
Cement, water, fine aggregates, coarse aggregates, mineral admixtures, and super plasticizers are used in high performance concrete. Concrete designed for high performance meets the structural and durability criteria by mixing the components in a particular ratio.
Concrete's performance can be enhanced by strengthening its paste phase, transition phase, and aggregate phase. The cement content should be increased, the water cement ratio should not exceed .3, and mineral admixtures and nonporous aggregates should be used.
Polymer Concrete
By adding polymers to it, polymer concrete is a unique kind of concrete that will minimize the pores in the member. The presence of air, water, or gel structure voids may be the cause of the concrete's porosity.
Polymer cement concrete
The members are allowed to cure and then dipped in high temperature monomer solutions to pack the voids through polymerization, just as the polymer-impregnated concrete.
Partially Impregnates and surface coated polymer concrete
The members are allowed to cure, just as the polymer impregnated concrete, and then submerged in high temperature monomer solutions to fill the gaps through polymerization.
To get more details, go through the following video tutorial.
Lecturer: civilogy
Polymer Impregnated Concrete
In this kind, regular concrete is given time to cure and solidify. Following this, high-temperature monomers including styrene, acrylonitrile, and thermoplastics are poured into the voids to pack them through polymerization.
The porosity of the member is reduced by using polymers instead of cement as binders. Polymer concrete is composed of polymers, aggregates, water, and coupling agents such as silane which improve bond strength. This concrete lacks strength because it lacks cement.
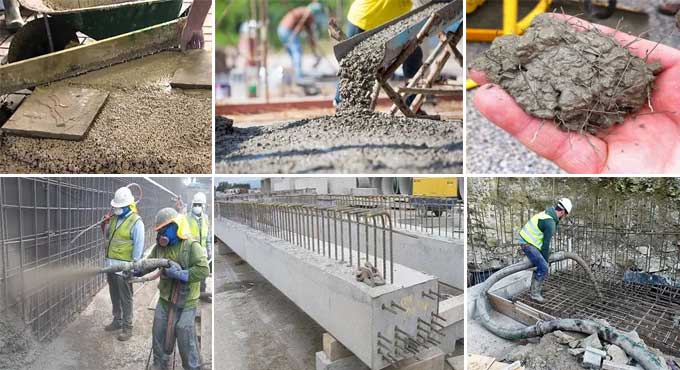